Hola holaaaa, hoy vamos a hablar de las herramientas y procesos necesarios para poder mecanizar piezasss.
1.Trazado y sus herramientas.
En el trazado se representa sobre la superficie de la pieza donde se debe mecanizar,aunque también se puede utilizar para verificar las piezas.
Formas de trazar.
-Trazado plano: Se marcan las lineas en la superficie plana de la pieza, es muy parecido a hacer un croquis, solo que en este se realiza en la pieza con los útiles de trazar.
-Trazado al aire: Se utiliza una punta de trazar montada en un gramil para marcar una o varias caras. El gramil se mueve por una superficie plana( Mármol de ajustador), lo que te permite trazar en varias dimensiones moviendo la pieza.
Instrumentos para trazar.
-Punta de trazar o trazador : Hace la función de un lápiz para trazar la pieza. Se trata de una varilla de acero templado afilada con un angulo de 30º, puede tener la forma de lápiz, o una varilla doblada,esta ultima forma se utiliza en el gramil.Punta de trazar |
Trazador |
-Compás: Sirve representar cualquier forma curva que tenga un centro, es parecido al compás que tienes muerto de risa por casa, solo que este esta hecho en acero templado.
-Granete: Sirve para hacer puntos de referencia para que apoye el compás o para realizar agujeros con el taladro, es una varilla cilíndrica hecha en acero templado y que tiene una punta cónica que tiene un angulo entre 60º y 120º.
-Gramil: Realiza la función de soporte para la punta de trazar, consta de una barra vertical u horizontal que esta montada sobre una base plana para poder moverlo por el mármol libremente.
-Calzos: Bloques con forma de V(que pesan como condenados para el tamaño que tienen) que sirven para aguantar piezas cilíndricas sobre el mármol.
-Cubos: También son bloques pero esta vez con forma de cubo (Soy un genio), y como los calzos te sirven de apoyo.
-Escuadras: Sirven para trazar lineas paralelas, perpendiculares o inclinadas. Están fabricadas en acero y tienen varias formas: Simples, de solapa o en T.
-Mármol: Es un soporte y guía para poder trazar las piezas en él. Esta hecho en hierro fundido, es plano y este si que pesa como un...
Trazado.
Antes de trazar.
-Lo primero que debes hacer es mirar el plano de la pieza y decidir el proceso para trazar.
-Medir la pieza para comprobar que tiene las medidas correctas.
-Quitar todo el oxido y si ya eres un pro echar una disolución para poder ver mejor el trazado.
-Calzar la pieza sobre el mármol para poder tener un apoyo correcto.
-Empezar a trazar en la mejor superficie que te permita trazar el mayor numero de lineas en la misma posición.
Orden de trazado.
-Trazar los ejes de la pieza.
-Trazar las lineas paralelas o perpendiculares a esos ejes.
-Trazar lineas curvas.
-Trazar los centros de las circunferencias y de los agujeros.
2.Sistemas y herramientas de control dimensional.
Instrumentos de medida directa.
En estos instrumentos el resultado de la medida se obtiene directamente del aparato.-Metro: Se trata de un instrumento de medida lineal y directa, su escala esta dividida en metros, centímetros y milímetros, tiene una apreciación máxima de un milímetro.
Para medir se coloca el inicio del metro con el borde de la pieza y fijarnos en la medida en el otro extremo de este.
Existen varios tipos de metros:
-Metro articulado: Varios brazos unidos por los extremos, se usa especialmente en carrocería.

-Metro flexible: Se trata de una cinta flexible de fibra o material textil graduada por ambos lados.
![]() |
Como el que tienen todas las madres en la caja de galletas/caja de la costura. |
-Flexómetro: Esta formado por una cinta flexible de acero graduada que se enrolla dentro de una caja.
-Reglas graduadas: Sirve para señalar, trazar y medir piezas. Esta hecha de acero, y las hay rígidas y flexibles, son rectangulares y tienen su escala.
Existen varios tipos de reglas(inserte broma aquí):
-Regla flexible: rígida y biselada: Tienen gran precisión en la medida.
-Regla angular: Para medir o trazar en superficies cilíndricas.
-Regla vertical: Permite trazar y medir piezas verticalmente (aplausos por favor).
-Regla de tacón: Tienen un tope que hace coincidir el inicio de la regla con la arista.
También las graduaciones pueden ser de varios tipos:
-Métrica por un lado.
-Métrica por ambos lados.
-Métrica por un lado y pulgadas por el otro.
-Calibre: Con este instrumento se pueden medir medidas interiores, exteriores y de profundidad con mucha precisión.Dependiendo del numero de divisiones del nonio sera mayor o menor su
apreciación.
Tiene varias partes:
-Boca fija: Es una regla de acero y en un extremo tiene una escuadra, es la que permite el movimiento de los demás componentes. Tiene dos escalas una en centímetros y milímetros y otra en pulgadas.
-Boca móvil: Ajustas sobre la boca fija, esta se mueve a través del palpador, que actúa de freno. Tiene unos biseles en los que está el nonio.
-Orejetas: Dos palpadores que se utilizan para medir interiores.
-Sonda:Se trata de una varilla que sirve para medir profundidad.
-Freno: Permite que una vez hayamos tomado la medida esta no se mueva.
Tipos de nonios:
-Nonio de 10 divisiones: Tiene una apreciación de 0.1 mm.
-Nonio de 20 divisiones: Tiene una apreciación de 0.05 mm.
-Nonio de 50 divisiones: Tiene una apreciación de 0.02 mm.
-Micrómetro: Realiza medidas de hasta 0.001 mm, aunque los mas utilizados son los de 0.01 mm, se trata de un tornillo que avanza sobre una tuerca fija. Es menos polivalente que un calibre, ya que si tienes un micrómetro de interiores solo vas a poder medir interiores.
Un micrómetro de exteriores tiene un cilindro fijo que esta graduado en milímetros, sobre el que se desplaza el tambor, esto esta unido a un cuerpo en forma de U en los dos extremos tiene las superficies de contactos una está fija y otra se puede mover.
Para medir se coloca la pieza entre las superficies de contacto y se cierra el micrómetro haciendo uso del trinquete que permite darle una presión.
Consta de dos escalas una superior en la que los milímetros están enteros y la inferior en la que están representados los medios milímetros.
Nos fijamos en la ultima raya que deja ver el tambor si se trata de una raya de la parte superior solo hay que sumarle la medida que te da en el tambor. Si se trata de una raya de la parte inferior se le suma 0.50 mm a la medida superior, y luego sumar también la medida del tambor.
-Transportador de ángulos: Sirve para medir los ángulos en grados te permite medir de 0º a 180º o de 180º a 0º. Esta formado por un semicírculo y una regla que gira en el centro del semicírculo.
-Goniómetro: También sirve para medir ángulos, pero la principal diferencia es que es capaz de medir 360º, este instrumento también se puede adaptar a herramientas de apriete, para poder medir el angulo de giro.
Instrumentos de medida indirecta.
-Reloj comparador: El reloj comparador permite apreciar centésimas de milímetro, cualquier desplazamiento del palpador se refleja en la escala principal. Para medir con el reloj comparador lo primero que se debe hacer es colocarlo en un soporte, acercar el palpador a la pieza y poner a cero el reloj, así ya estaría listo para medir.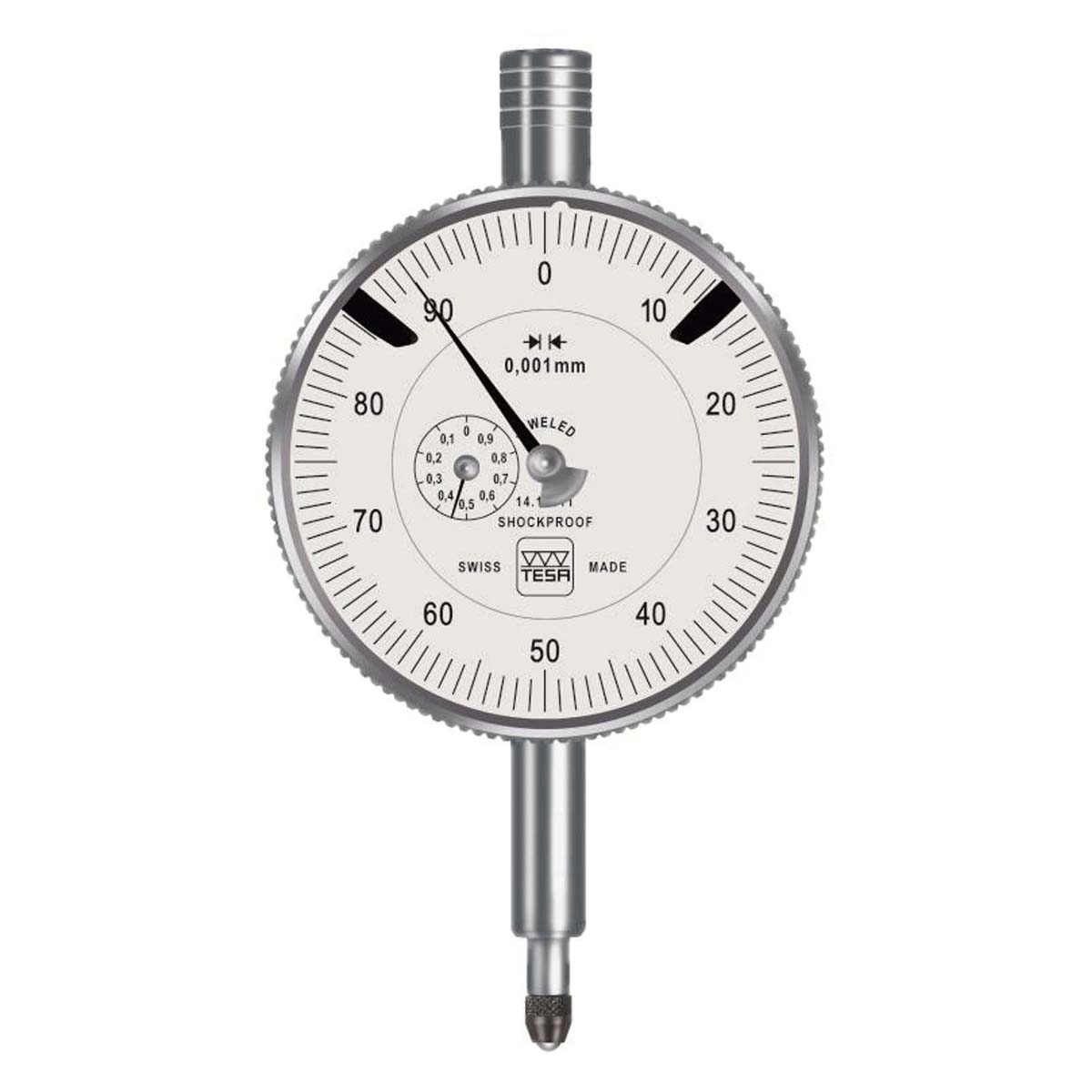
-Alexómetro: Se utiliza para medir interiores, es necesario un reloj comparador. Tiene su palpador, que transmite los movimientos al reloj comparador. Para medir se desplaza el alexómetro de izquierda a derecha, y en el punto de inflexión se encuentra la medida.
-Galgas de espesores: Se trata de unas laminas de distintos espesores, sirve para medir la separación entre dos piezas pasando la lamina entre las piezas y viendo si pasa o no pasa.
-Calibres de diámetros: Son varillas muy pequeñas que están calibradas para medir pasos calibrados.
-Calibres pasa no pasa: Sirve para medir diámetros muy precisos, son mas fiables y fáciles de usar que los micrómetros.

-Peines de rosca: Consta de un conjunto de chapas en las que están tallados los perfiles de las roscas, para así saber su paso. Normalmente son dobles, por un lado miden métrica y por el otro Whitworth.
3.Limado.
Esta técnica se utiliza para rebajar las superficies, mediante el arranque de viruta, se puede realizar de dos formas: manual o mecánico.Limado manual.
Lima: Se trata de una pletina de acero templado extraduro que tiene tallados unos dientes para que pueda arrancar virutas cuando avanza. Consta de varias partes: Mango, cola, talón, cuerpo y la cabeza.
Picado: Es el grado de rugosidad que tiene el cuerpo de la lima. El mas común es el de picado doble.
Hay varios tipos de picado:
-Lima sencilla recta: Recomendable para igualar superficies y se emboza con facilidad. Se puede utilizar en metales blandos.
- Lima picado doble: Dos tallas una entre 35º y 45º y otra entre 70º y 80º. Se utiliza en metales duros.
-Lima picado para madera, escofina: Los dientes están separados (¿Hace falta que diga para que se utiliza?)
-Lima picado especial: Ranuras en forma de curva, se utiliza para ajustes.
Forma:Hay diferentes tipos dependiendo de la superficie en la que vayas a trabajar.
-Plana:Para superficies planas (tremenda aclaración).
-Triangulares:Para superficies con ángulos que superen los 60º y también para superficies planas.
-Cuadradas:Superficies cuadradas, ángulos de 90º, ranuras....
-Media caña:Superficies curvas y planas.
-Redondas:Superficies cóncavas.
-De cuchillo:Superficies con ángulos menores de 60º o para esquinas.
Tamaño:La distancia que hay desde el talón hasta el extremo de la lima, se expresa en pulgadas.
Grado de corte: Numero de dientes por centímetro cuadrado.
Hay varios tipos de grado de corte:
-Extrafinas: Mas de 16 dientes, se utiliza para darle el acabado.
-Finas: 16 dientes, como las extrafinas se utilizan para dar el acabado.
-Semi-finas: 12 dientes, para alisar o preparar la superficie.
-Bastas: 8 dientes, para comenzar a limar.
-Ásperas: 6 dientes, como las bastas también se utilizan para comenzar a limar.
Proceso de limado.
-Se coloca la pieza bien centrada y fijada en un tornillo de banco.
-Se elige la lima según la dureza del material y el acabado que se desea, no cojas una lima que esta embozada o el picado este dañado y nunca utilizar limas que han sido manchadas con aceites o grasas.
-El tronco del operario debe moverse ligeramente, el ritmo debe ser de entre 50 y 60 golpes por minuto.
-La lima se sujeta con la mano derecha en el mango con el dedo pulgar por encima y los demas dedos rodeando el mango, en caso de que seas diestro, con la mano izquierda se sujeta el extremo de la lima.
-Utilizar toda la longitud de la lima y evitar tocar con las manos la superficie limada ni la lima.
-Se debe presionar levemente la lima cuando avanza, en superficies planas se deben cruzar los trazos para que así sea mas uniforme.
4.Serrado manual.
Con movimientos lineales de la sierra de mano gracias al operario se consigue un corte.
La sierra de mano, consta de varias partes:
Arco: Se trata del soporte de la hoja, tiene forma de U y en sus extremos tiene unos tacos para sujetar la hoja.
Hoja: Lamina delgada de acero al carbono o aceros rápidos, tiene un dentado y en sus extremos tiene dos agujeros para poder colocarla en el arco. Tienen varias características:
- Tamaño: La longitud que es la medida en pulgadas que hay entre los agujeros.
El ancho, que es la distancia entre los dos lados, que puede estar dada en pulgadas o milímetros.
El espesor, que normalmente es de 0.65 mm o 0.90 mm.
- Paso: Longitud entre dos crestas de dos dientes consecutivos, si el material es blando el paso es mayor. Se expresa en numero de dientes por pulgada, pudiendo ser fino, medio o basto.
- Triscado: Es la forma en la que están situados los dientes, evita que se atasque y facilita el corte.
Cordones de sierra: Se trata de partículas de tungsteno pegadas a un cordón de aleación de acero. El corte se realiza por abrasión y permite la realización de cortes curvos. Consta de varias ventajas: No se embota, se desafila ni se rompe, corta tanto hacia delante como hacia atrás.
Proceso de serrado.
Antes de serrar:
-Se debe escoger una hoja en función del material y del espesor de la pieza que se quiere cortar.
-La hoja debe estar limpia.
-La pieza tiene que estar bien sujeta.
Serrado:
-El operario debe estar en una posición cómoda, pudiendo mover el tronco ligeramente.
-El ritmo debe de ser: Entre 30 y 40 golpes por minutos para materiales duros y entre 50 y 60 golpes por minuto para materiales blandos.
-El mango se sujeta con la mano derecha si eres diestro y con la mano izquierda se sujeta el extremo para que no tenga balanceo.
-Al empezar el corte se hace una muesca para así guiar a la hoja.
-Se presiona suavemente la sierra cuando avanza intentando usar la mayor cantidad de dientes posibles, para retroceder no haremos presión.
5.Taladrado.
El taladrado consiste en un corte mediante el arranque de virutas que permite hacer agujeros.
Tipos de taladros.
Los taladros son los encargados de transmitir el giro a la broca y los hay de varios tipos:
-Taladro portátil manual: (berbiquíes) Es el operario el que realiza el esfuerzo para que la broca gire.
-Taladro portátil eléctrico: Estos pueden tener batería o no, los que no tienen deben estar conectados a la red eléctrica.
-Taladro portátil neumático: Este tipo de taladro necesita de aire comprimido, tienen varias ventajas sobre los demás, son silenciosos, económicos y pesan menos. El inconveniente es que necesita ser lubricado para evitar el oxido.
-Rotalines: Pueden alcanzar muchas revoluciones y se utiliza para ajustar una pieza. Utiliza brocas de entre 0.5 y 2.5 mm y también fresas pequeñas.
-Taladros fijos: Permiten realizar el taladrado cómodamente y con mucha precisión. Tienen un sistema de poleas que permite variar la velocidad de giro, también tiene una manivela para poder ajustar el avance de la broca. Aquí podemos clasificar los de columna y sobremesa, la diferencia entre estas dos es que el de columna permite realizar agujeros en piezas mayores, ambos tienen transmisión por polea o engranajes.

Taladro de sobremesa

Taladro de columna.
También existe otro tipo de taladro fijo de bandera o radial, siendo muy parecido al de columna, solo que este tiene un husillo que permite girar alrededor de la columna permitiendo taladrar en cualquier parte que alcance el husillo.
Tipos de amarre de la broca.
Portabrocas: Mediante una llave especial se ajusta el cierre de las mordazas, en algunos taladros es desmontable y se puede intercambiar.
Cono Morse: Se trata de conos de distinto tamaño que se encajan entre si, permite acoplar brocas cónicas y portabrocas.
Con movimientos lineales de la sierra de mano gracias al operario se consigue un corte.
La sierra de mano, consta de varias partes:
Arco: Se trata del soporte de la hoja, tiene forma de U y en sus extremos tiene unos tacos para sujetar la hoja.
Hoja: Lamina delgada de acero al carbono o aceros rápidos, tiene un dentado y en sus extremos tiene dos agujeros para poder colocarla en el arco. Tienen varias características:
- Tamaño: La longitud que es la medida en pulgadas que hay entre los agujeros.
El ancho, que es la distancia entre los dos lados, que puede estar dada en pulgadas o milímetros.
El espesor, que normalmente es de 0.65 mm o 0.90 mm.
- Paso: Longitud entre dos crestas de dos dientes consecutivos, si el material es blando el paso es mayor. Se expresa en numero de dientes por pulgada, pudiendo ser fino, medio o basto.
- Triscado: Es la forma en la que están situados los dientes, evita que se atasque y facilita el corte.
Proceso de serrado.
Antes de serrar:
-Se debe escoger una hoja en función del material y del espesor de la pieza que se quiere cortar.
-La hoja debe estar limpia.
-La pieza tiene que estar bien sujeta.
Serrado:
-El operario debe estar en una posición cómoda, pudiendo mover el tronco ligeramente.
-El ritmo debe de ser: Entre 30 y 40 golpes por minutos para materiales duros y entre 50 y 60 golpes por minuto para materiales blandos.
-El mango se sujeta con la mano derecha si eres diestro y con la mano izquierda se sujeta el extremo para que no tenga balanceo.
-Al empezar el corte se hace una muesca para así guiar a la hoja.
-Se presiona suavemente la sierra cuando avanza intentando usar la mayor cantidad de dientes posibles, para retroceder no haremos presión.
5.Taladrado.
El taladrado consiste en un corte mediante el arranque de virutas que permite hacer agujeros.
Tipos de taladros.
Los taladros son los encargados de transmitir el giro a la broca y los hay de varios tipos:
-Taladro portátil manual: (berbiquíes) Es el operario el que realiza el esfuerzo para que la broca gire.
-Taladro portátil eléctrico: Estos pueden tener batería o no, los que no tienen deben estar conectados a la red eléctrica.
-Taladro portátil neumático: Este tipo de taladro necesita de aire comprimido, tienen varias ventajas sobre los demás, son silenciosos, económicos y pesan menos. El inconveniente es que necesita ser lubricado para evitar el oxido.
-Rotalines: Pueden alcanzar muchas revoluciones y se utiliza para ajustar una pieza. Utiliza brocas de entre 0.5 y 2.5 mm y también fresas pequeñas.
-Taladros fijos: Permiten realizar el taladrado cómodamente y con mucha precisión. Tienen un sistema de poleas que permite variar la velocidad de giro, también tiene una manivela para poder ajustar el avance de la broca. Aquí podemos clasificar los de columna y sobremesa, la diferencia entre estas dos es que el de columna permite realizar agujeros en piezas mayores, ambos tienen transmisión por polea o engranajes.
Taladro de sobremesa |
Taladro de columna. |
Tipos de amarre de la broca.
Portabrocas: Mediante una llave especial se ajusta el cierre de las mordazas, en algunos taladros es desmontable y se puede intercambiar.
Cono Morse: Se trata de conos de distinto tamaño que se encajan entre si, permite acoplar brocas cónicas y portabrocas.
Sujeción de la pieza.
La pieza se sujeta con un tornillo, si tiene piezas que permiten movimiento se amarran con mordazas, tiene que estar bien ajustado ya que si no la pieza podría soltarse y hacer daño a alguien.
Herramientas de corte.
Brocas: Está fabricada en acero aleado con metales duros, tiene una forma cilíndrica y unas ranuras helicoidales que acaban en aristas, llamados labios.
Tienen varias partes:
-Punta: Es la parte que corta, tiene dos filos, uno transversal que rasca la pieza y el labio que inicia el corte. Tienen que tener un angulo de 55º.
-Cuerpo: Sección entre el filo y mango, tiene hechas unas ranuras helicoidales para poder evacuar la viruta.
-Mango o cola: Es la parte que ajusta en el taladro, los hay cilíndricos o cónicos (Para los que llevan cono morse).
-Cuello: Es la parte en la que lleva grabadas las características.
Dependiendo del material que se vaya a taladrar el angulo de la punta de las brocas varia:
-120º: Para metales duros (Cobre, acero y fundiciones).
-De 60º a 90º: Plásticos.
-De 40º a 60º: Aleaciones blandas (Aluminio, manganeso).
También varia el material de las brocas, hay de varios tipos:
-Acero al carbono HS: Tiene un porcentaje de carbono de entre 0.65 y 1.5%, ademas tiene un 0.35% de manganeso y otro tanto de silicio.
-Acero rápido HSS: Es acero con un porcentaje de carbono del 0.75 al 0.95%, que esta aleado con cromo 3.5 a 4.5%, molibdeno 1 a 9%, vanadio 1 al 2%, wolframio 2 al 17% y cobalto 5 al 8.75%.
-Acero rapido HSS titanio rectificadas: Como las anteriores, solo que tienen una cobertura de titanio, que permite tener mucha precisión y taladrar acero inoxidable.
-Acero rapido HSS cobalto rectificadas: Son las que tienen mayor calidad, con ellas se puede trabajar los materiales mas duros y trabajar con altas temperaturas.
-Fresas: Están hechas con un rebaje angular y tienen varias estrías. Las hay de dos tipos:
-De acero: Están fabricadas en acero y en la parte cónica lleva estrías y filos.
-Abrasivas: Están fabricadas con piedra esmeril, las hay con varios tipos de grano y su duración es limitada.
-Escariador: Estan fabricadas en acero templado y sirve para alisar y dejar con un acabado de calidad el agujero que se ha realizado con el taladro. Hay varios tipos:
-Espiral a izquierdas: Para agujeros pasantes.
-Espiral recta o a derechas: Para agujeros ciegos.
Afilado y mantenimiento de la herramienta de corte.
Se realiza con una esmeril.
-Se apoya la broca en el soporte para que no se mueva.
-Se sitúa la piedra con un angulo que es la mitad del angulo del vértice, para que así los labios tengan el mismo angulo.
-Se gira a la derecha o la izquierda para así formar un cono en la punta, recordad que tiene que tener un angulo entre el filo transversal y los labios de 55º.
Procedimiento de corte con taladro y medidas de seguridad.
Bueno empezaré por las normas de seguridad.
-Se debe tener puestas las gafas (Para evitar proyecciones a los ojos), guantes (Si eres de los que no quiere ponérselos también puedes ya que existe el riesgo de que te enganche la broca el guante y te quedes sin mano) y si ya eres un pro coges y te pones un peto ( Para evitar proyecciones al cuerpo).
-La pieza debe estar bien apretada( No me cansaré de decirlo).
- Se debe tener mucho cuidado cuando la broca va a salir ya que se puede quedar enganchada y romperse.
-No se debe sujetar la pieza con las manos ( Lógico no??).
- No tocar la herramienta después de taladrar ya que estará bien caliente.
- Una vez acabado se debe limpiar las virutas y los útiles de corte y guardarlos.
Proceso de taladrado:
- Se traza el centro y se le da un granetazo para que la broca entre en el sitio.
- Se fija la pieza en el tornillo para que no se mueva ( No se cuantas veces lo he dicho).
- Si el agujero es mayor de 10mm es recomendable hacer un taladro que sea la mitad del taladro final.
- Se selecciona la velocidad adecuada, que depende del material y de la broca que vayamos a usar.
- Se ajusta la profundidad si la maquina tiene ese ajuste y si no se marca la broca con un trozo de cinta aislante para saber donde dejar de taladrar.
-Se comienza el taladrado teniendo mucho cuidado al principio y si es necesario se refrigera con taladrina.
Mantenimiento de equipos.
- Limpiar el taladro de virutas y restos de refrigerante.
- Controlar el nivel de aceite si lleva transmisión por engranajes.
-Engrasar en los puntos de engrase según te diga el manual.
-Comprobar el juego que tiene el husillo y si es necesario ajustarle.
6.Roscado.
Se trata de mecanizar por arranque de viruta una rosca en un cilindro interior o exterior.
Tipos de rosca.
-Métrica: Tiene un filete en forma de triangulo equilatero con las crestas truncadas 1/16 de altura y los fondos redondeados, como inconveniente es que tiene un pequeño juego debido a las crestas truncadas. Se mide en milímetros.
-Whitworth: Los flancos de los filetes son de 55º y tiene forma de triangulo isósceles, las crestas y los fondos son redondeados. Se mide en pulgadas.
-Gas: Es muy parecida a la Whitworth, solo que esta es de paso fino, se utiliza en tuberías de fluidos de hidráulica y neumática.
-Sellers o americana: Parecida a la métrica, solo que tiene las crestas truncadas 1/8 de altura. Se mide en pulgadas.
-Chapa: Forma triangular o trapezoidal, con un paso muy ancho para así adaptarse a plásticos o chapas. No necesita tuerca, pero no aguanta grandes esfuerzos. Se utiliza principalmente en carrocería.
Machos de roscar.
Sirven para la realización de roscas interiores, están fabricados en acero rápido con aleación de entre un 3 y un 5% de cobalto o vanadio. Tienen forma de tornillo y tienen unas aristas longitudinales que permiten cortar el material. Tienen varias partes:
-Entrada: Inicia y centra la rosca.
-Cuerpo: Es la parte que hace la rosca.
-Mango: En el lleva la cabeza cuadrada para sujetarle al giramachos.
Procedimiento:
- Después del taladrado del agujero que se va a roscar se avellana la entrada de 60 a 120º.
- Se pone el macho numero 1 en el giramachos y se coloca perpendicular a la pieza.
- Se gira en el sentido de avance que se le quiera dar, por cada media vuelta se da un cuarto en sentido contrario para así romper las virutas, se debe lubricar.
- Una vez se ha pasado el macho numero 1 se debe hacer la misma operación con el macho intermedio y el de acabado.
Terrajas o cojinetes de roscar.
Sirve para realizar roscas exteriores, están fabricadas en acero al carbono o acero rápido. En el interior lleva practicada una rosca con ranuras longitudinales, que son las que cortan el material. La entrada lleva un avellanado de 60 a 120º para facilitar el inicio y centrado.
Procedimiento:
-Se realiza un achaflanado a 45º en la varilla que se quiere roscar para ayudar al inicio y para que la terraja agarre material.
-Se pone la terraja en el portaterrajas y se coloca perpendicular a la pieza.
-Se gira en el sentido de avance que se le quiera dar, por cada media vuelta dar un cuarto en sentido contrario para romper las virutas.
Este proceso se realiza en solo una pasada por lo que tiene que estar bien lubricado y tener mucho cuidado.
Y bueno aqui se acaba esta entrada que tan poco me ha costado haceer paaaz.
Herramientas de corte.
Brocas: Está fabricada en acero aleado con metales duros, tiene una forma cilíndrica y unas ranuras helicoidales que acaban en aristas, llamados labios.
Tienen varias partes:
-Punta: Es la parte que corta, tiene dos filos, uno transversal que rasca la pieza y el labio que inicia el corte. Tienen que tener un angulo de 55º.
-Cuerpo: Sección entre el filo y mango, tiene hechas unas ranuras helicoidales para poder evacuar la viruta.
-Mango o cola: Es la parte que ajusta en el taladro, los hay cilíndricos o cónicos (Para los que llevan cono morse).
-Cuello: Es la parte en la que lleva grabadas las características.
Dependiendo del material que se vaya a taladrar el angulo de la punta de las brocas varia:
-120º: Para metales duros (Cobre, acero y fundiciones).
-De 60º a 90º: Plásticos.
-De 40º a 60º: Aleaciones blandas (Aluminio, manganeso).
También varia el material de las brocas, hay de varios tipos:
-Acero al carbono HS: Tiene un porcentaje de carbono de entre 0.65 y 1.5%, ademas tiene un 0.35% de manganeso y otro tanto de silicio.
-Acero rápido HSS: Es acero con un porcentaje de carbono del 0.75 al 0.95%, que esta aleado con cromo 3.5 a 4.5%, molibdeno 1 a 9%, vanadio 1 al 2%, wolframio 2 al 17% y cobalto 5 al 8.75%.
-Acero rapido HSS titanio rectificadas: Como las anteriores, solo que tienen una cobertura de titanio, que permite tener mucha precisión y taladrar acero inoxidable.
-Acero rapido HSS cobalto rectificadas: Son las que tienen mayor calidad, con ellas se puede trabajar los materiales mas duros y trabajar con altas temperaturas.
-Fresas: Están hechas con un rebaje angular y tienen varias estrías. Las hay de dos tipos:
-De acero: Están fabricadas en acero y en la parte cónica lleva estrías y filos.
-Abrasivas: Están fabricadas con piedra esmeril, las hay con varios tipos de grano y su duración es limitada.
-Escariador: Estan fabricadas en acero templado y sirve para alisar y dejar con un acabado de calidad el agujero que se ha realizado con el taladro. Hay varios tipos:
-Espiral a izquierdas: Para agujeros pasantes.
-Espiral recta o a derechas: Para agujeros ciegos.
Afilado y mantenimiento de la herramienta de corte.
Se realiza con una esmeril.
-Se apoya la broca en el soporte para que no se mueva.
-Se sitúa la piedra con un angulo que es la mitad del angulo del vértice, para que así los labios tengan el mismo angulo.
-Se gira a la derecha o la izquierda para así formar un cono en la punta, recordad que tiene que tener un angulo entre el filo transversal y los labios de 55º.
Procedimiento de corte con taladro y medidas de seguridad.
Bueno empezaré por las normas de seguridad.
-Se debe tener puestas las gafas (Para evitar proyecciones a los ojos), guantes (Si eres de los que no quiere ponérselos también puedes ya que existe el riesgo de que te enganche la broca el guante y te quedes sin mano) y si ya eres un pro coges y te pones un peto ( Para evitar proyecciones al cuerpo).
-La pieza debe estar bien apretada( No me cansaré de decirlo).
- Se debe tener mucho cuidado cuando la broca va a salir ya que se puede quedar enganchada y romperse.
-No se debe sujetar la pieza con las manos ( Lógico no??).
- No tocar la herramienta después de taladrar ya que estará bien caliente.
- Una vez acabado se debe limpiar las virutas y los útiles de corte y guardarlos.
Proceso de taladrado:
- Se traza el centro y se le da un granetazo para que la broca entre en el sitio.
- Se fija la pieza en el tornillo para que no se mueva ( No se cuantas veces lo he dicho).
- Si el agujero es mayor de 10mm es recomendable hacer un taladro que sea la mitad del taladro final.
- Se selecciona la velocidad adecuada, que depende del material y de la broca que vayamos a usar.
- Se ajusta la profundidad si la maquina tiene ese ajuste y si no se marca la broca con un trozo de cinta aislante para saber donde dejar de taladrar.
-Se comienza el taladrado teniendo mucho cuidado al principio y si es necesario se refrigera con taladrina.
Mantenimiento de equipos.
- Limpiar el taladro de virutas y restos de refrigerante.
- Controlar el nivel de aceite si lleva transmisión por engranajes.
-Engrasar en los puntos de engrase según te diga el manual.
-Comprobar el juego que tiene el husillo y si es necesario ajustarle.
6.Roscado.
Se trata de mecanizar por arranque de viruta una rosca en un cilindro interior o exterior.
Tipos de rosca.
-Métrica: Tiene un filete en forma de triangulo equilatero con las crestas truncadas 1/16 de altura y los fondos redondeados, como inconveniente es que tiene un pequeño juego debido a las crestas truncadas. Se mide en milímetros.
-Whitworth: Los flancos de los filetes son de 55º y tiene forma de triangulo isósceles, las crestas y los fondos son redondeados. Se mide en pulgadas.
-Gas: Es muy parecida a la Whitworth, solo que esta es de paso fino, se utiliza en tuberías de fluidos de hidráulica y neumática.
-Sellers o americana: Parecida a la métrica, solo que tiene las crestas truncadas 1/8 de altura. Se mide en pulgadas.
-Chapa: Forma triangular o trapezoidal, con un paso muy ancho para así adaptarse a plásticos o chapas. No necesita tuerca, pero no aguanta grandes esfuerzos. Se utiliza principalmente en carrocería.
Machos de roscar.
Sirven para la realización de roscas interiores, están fabricados en acero rápido con aleación de entre un 3 y un 5% de cobalto o vanadio. Tienen forma de tornillo y tienen unas aristas longitudinales que permiten cortar el material. Tienen varias partes:
-Entrada: Inicia y centra la rosca.
-Cuerpo: Es la parte que hace la rosca.
-Mango: En el lleva la cabeza cuadrada para sujetarle al giramachos.
Procedimiento:
- Después del taladrado del agujero que se va a roscar se avellana la entrada de 60 a 120º.
- Se pone el macho numero 1 en el giramachos y se coloca perpendicular a la pieza.
- Se gira en el sentido de avance que se le quiera dar, por cada media vuelta se da un cuarto en sentido contrario para así romper las virutas, se debe lubricar.
- Una vez se ha pasado el macho numero 1 se debe hacer la misma operación con el macho intermedio y el de acabado.
Terrajas o cojinetes de roscar.
Sirve para realizar roscas exteriores, están fabricadas en acero al carbono o acero rápido. En el interior lleva practicada una rosca con ranuras longitudinales, que son las que cortan el material. La entrada lleva un avellanado de 60 a 120º para facilitar el inicio y centrado.
Procedimiento:
-Se realiza un achaflanado a 45º en la varilla que se quiere roscar para ayudar al inicio y para que la terraja agarre material.
-Se pone la terraja en el portaterrajas y se coloca perpendicular a la pieza.
-Se gira en el sentido de avance que se le quiera dar, por cada media vuelta dar un cuarto en sentido contrario para romper las virutas.
Este proceso se realiza en solo una pasada por lo que tiene que estar bien lubricado y tener mucho cuidado.
Y bueno aqui se acaba esta entrada que tan poco me ha costado haceer paaaz.
No hay comentarios:
Publicar un comentario